芯片制造专用电源技术要求
芯片制造专用电源是为半导体生产线中关键工艺设备提供精准电能的核心部件,其技术要求涵盖以下核心维度:
1. 高精度与稳定性
- 电流/电压控制精度:需达到±0.1%的纹波抑制能力(如射频电源纹波控制在±0.2%以内),确保等离子体激发和刻蚀工艺的均匀性 。
- 动态响应速度:微秒级调节能力,适应离子注入、刻蚀等高动态工艺需求 。
- 多参数协同控制:支持电压、频率、脉冲宽度等参数的实时协同调节(如刻蚀设备需匹配2MHz-60MHz射频频率) 。
2. 高频与高效能
- 射频电源需覆盖2MHz-60MHz高频段,采用同步DC/DC转换技术,效率超过85% 。
- 功率密度提升,如激光驱动电源需支持10W-500W输出,电光转换效率达40%以上 。
3. 抗干扰与安全防护
- EMC设计:符合半导体厂房的防静电标准(如GB 50809-2012规范要求接地电阻≤1Ω) 。
- 多重保护机制:集成过压、过流、温度监测及防爆设计,应对特种气体(如硅烷)泄漏风险 。
4. 智能化与兼容性
- 支持IoT远程监控(如参数云端存储、异常报警),兼容RS232/RS485通信协议,实现与设备主控系统的无缝对接 。
- 模块化设计,支持48路同步输出,适配大功率产线扩展需求 。
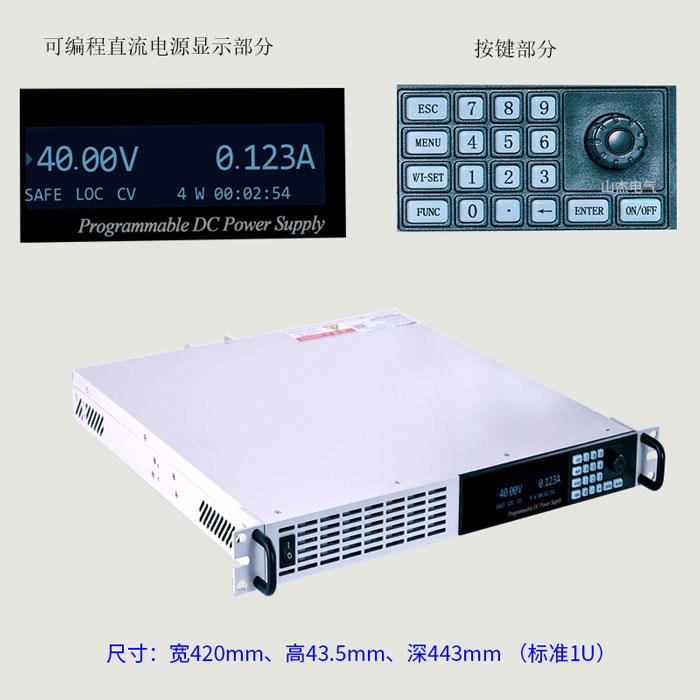
主要应用场景
芯片制造专用电源在半导体生产全流程中发挥关键作用,具体场景包括:
1. 刻蚀设备
- 应用:干法刻蚀(如等离子体刻蚀)中,射频电源通过高频电场激发等离子体,实现纳米级材料去除。
- 技术要求:阻抗匹配精度≤5%,脉冲宽度调节范围0.1μs-10ms 。
2. 薄膜沉积设备
- 应用:PECVD、ALD等工艺中,驱动射频源生成均匀等离子体,控制薄膜厚度与应力。
- 案例:中芯国际产线采用全固态射频电源,提升氮化硅薄膜沉积速率15% 。
3. 离子注入机
- 应用:高能离子束注入需高压电源(如500kV)加速粒子,掺杂精度直接影响芯片电性能。
- 技术突破:自适应脉冲技术(FinFET工艺)实现掺杂浓度误差≤3% 。
4. 光刻与激光加工
- 应用:光刻机激光驱动电源需波长稳定(如193nm DUV光源),功率波动≤0.5% 。
- 扩展场景:激光退火、晶圆标记等工艺 。
5. 测试与封装
- 应用:晶圆测试设备需低噪声电源(如LDO稳压器),噪声抑制比≥70dB 。
- 封装工艺:激光焊锡电源支持0.03mm光斑精度,提升焊点良率 。
技术发展趋势
- 高频化与集成化:GaN/SiC器件推动射频电源频率突破100MHz,体积缩小30% 。
- 绿色节能:数据中心电源管理芯片向95%能效升级,符合“东数西算”政策要求 。
- AI赋能控制:结合深度学习算法优化等离子体参数预测(如匹配网络寿命延长20%) 。
- 材料创新:散热结构从风冷向液冷演进,支持3.6kW以上高功率场景 。
总结
芯片制造专用电源是半导体产业的核心“能源引擎”,其技术迭代直接关联制程精度与产能。未来,随着第三代半导体材料与智能化技术的融合,该类电源将在3nm以下先进制程、量子芯片等前沿领域发挥更大价值